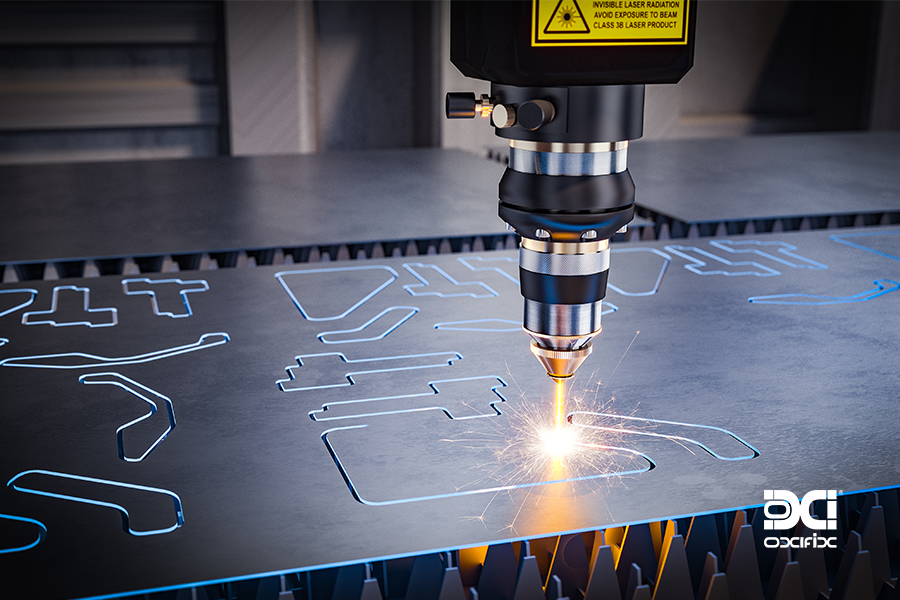
Os processos de usinagem não convencionais representam um avanço significativo na fabricação de peças e componentes industriais. Esses métodos inovadores surgiram como resposta à necessidade de trabalhar com materiais mais duros e complexos, bem como para alcançar níveis de precisão e eficiência superiores aos métodos tradicionais.
Nas últimas décadas, a importância desses processos tem crescido exponencialmente, impulsionada pela demanda por produtos de alta qualidade e pela evolução das tecnologias de fabricação. Eles oferecem soluções que muitas vezes são impossíveis ou impraticáveis com as técnicas de usinagem convencionais.
O objetivo deste artigo é discutir e explorar os diferentes tipos de processos de usinagem não convencionais, como usinagem a laser, usinagem ultrassônica, usinagem eletroquímica, roller burnishing, usinagem por jato de água e usinagem híbrida. Além disso, vamos abordar outros processos menos comuns que também desempenham um papel crucial na indústria moderna.
Usinagem a Laser
A usinagem a laser é um processo inovador que utiliza um feixe de laser de alta intensidade para remover material de uma peça de trabalho. Este método é particularmente eficaz para criar cortes precisos e detalhados, bem como para gravar e marcar superfícies com extrema precisão.
Como Funciona o Processo de Usinagem a Laser
O processo de usinagem a laser envolve a emissão de um feixe de luz concentrado, que é direcionado para a superfície do material. A alta intensidade do feixe de laser gera temperaturas elevadas, suficientes para derreter e vaporizar o material na área focalizada. Esse processo pode ser controlado com extrema precisão, permitindo a remoção de material em níveis micrométricos.
Benefícios do Uso de Alta Temperatura para Derreter e Vaporizar Materiais
- Precisão Extrema: A capacidade de focar o feixe de laser em áreas muito pequenas permite cortes e gravações altamente precisos.
- Versatilidade: A usinagem a laser pode ser aplicada em uma ampla variedade de materiais, incluindo metais, plásticos, cerâmicas e compósitos.
- Velocidade e Eficiência: O uso de altas temperaturas para derreter e vaporizar materiais permite que o processo seja realizado rapidamente, aumentando a eficiência da produção.
- Qualidade de Acabamento: A precisão do feixe de laser resulta em bordas limpas e suaves, reduzindo a necessidade de retrabalho e acabamento adicional.
Exemplos de Aplicação em Produção de Ferramentas de Corte
A usinagem a laser é amplamente utilizada na produção de ferramentas de corte devido à sua capacidade de criar geometrias complexas e precisas. Alguns exemplos de aplicação incluem:
Aplicação | Descrição |
Produção de Brocas | Cortes precisos e afiados para brocas de alta performance. |
Fabricação de Facas Industriais | Criação de lâminas com bordas finas e uniformes, garantindo cortes limpos e eficientes. |
Ferramentas de Usinagem CNC | Desenvolvimento de ferramentas com geometrias complexas para operações de fresamento e torneamento CNC. |
Usinagem Ultrassônica
A usinagem ultrassônica é um método de remoção de material que utiliza vibrações de alta frequência combinadas com um líquido abrasivo. Este processo é especialmente eficaz para materiais frágeis e duros, onde métodos convencionais podem causar danos ou não serem viáveis.
Descrição do Processo de Usinagem Ultrassônica
O processo de usinagem ultrassônica envolve a aplicação de vibrações mecânicas de alta frequência, tipicamente na faixa de 20 a 40 kHz, a uma ferramenta de usinagem. A ferramenta, em contato com a peça de trabalho, é acompanhada por um líquido abrasivo que contém partículas finas. Quando a ferramenta vibra, as partículas abrasivas na suspensão são empurradas contra a superfície do material, removendo-o de maneira controlada e precisa.
Vantagens do Uso de Vibração e Líquido Abrasivo
- Precisão e Controle: A usinagem ultrassônica permite uma remoção de material extremamente precisa, ideal para aplicações que exigem alto nível de detalhamento.
- Baixa Força de Corte: O uso de vibrações de alta frequência reduz a força de corte necessária, minimizando o risco de danificar materiais frágeis.
- Versatilidade de Materiais: Pode ser aplicada a uma ampla gama de materiais, incluindo cerâmicas, vidros, e metais duros.
- Redução de Calor: O líquido abrasivo ajuda a dissipar o calor gerado durante o processo, evitando deformações térmicas na peça de trabalho.
Indicação para Materiais Frágeis e Duros
A usinagem ultrassônica é particularmente indicada para materiais que são difíceis de usinar com métodos convencionais devido à sua fragilidade ou dureza. Alguns exemplos comuns incluem:
Material | Aplicação |
Cerâmicas | Componentes eletrônicos, isoladores térmicos e revestimentos resistentes ao desgaste. |
Vidros | Lentes ópticas, telas de dispositivos eletrônicos e artefatos decorativos. |
Metais Duros | Ferramentas de corte, matrizes e componentes de motores. |
Usinagem Eletroquímica
A usinagem eletroquímica (ECM) é um processo avançado de remoção de material que utiliza reações químicas controladas para usinar peças de trabalho em nível atômico. Esse processo é altamente eficiente e preciso, tornando-se uma escolha ideal para aplicações que exigem tolerâncias rigorosas e superfícies de alta qualidade.
Como Ocorre a Usinagem Eletroquímica
O processo de usinagem eletroquímica envolve a aplicação de uma corrente elétrica entre a peça de trabalho e uma ferramenta de eletrodo, imersos em um eletrólito. A peça de trabalho atua como o ânodo, enquanto a ferramenta de eletrodo atua como o cátodo. Quando a corrente elétrica é aplicada, ocorre uma reação eletroquímica que dissolve o material da peça de trabalho de maneira controlada, sem contato direto entre a ferramenta e a peça.
Os principais componentes do processo ECM incluem:
- Fonte de Energia: Fornece a corrente elétrica necessária para a reação eletroquímica.
- Ferramenta de Eletrodo: Configurada para a forma desejada da usinagem, agindo como o cátodo.
- Eletrólito: Solução condutora que facilita a reação eletroquímica entre a peça de trabalho e o eletrodo.
Benefícios de Controlar as Reações Químicas para Remover Material
- Precisão Extrema: A ECM permite a remoção de material em nível atômico, resultando em superfícies extremamente precisas e acabamentos impecáveis.
- Ausência de Desgaste da Ferramenta: Como não há contato direto entre a ferramenta e a peça de trabalho, o desgaste da ferramenta é praticamente inexistente.
- Processamento de Materiais Difíceis de Usinar: ECM é ideal para materiais que são difíceis de usinar por métodos convencionais, como ligas resistentes ao calor, titânio e superligas.
- Baixa Tensão Mecânica: A ausência de forças de corte mecânicas reduz o risco de deformações e tensões residuais na peça de trabalho.
Aplicações em Nível Atômico
A usinagem eletroquímica é amplamente utilizada em indústrias que exigem precisão e qualidade de superfície superiores. Alguns exemplos de aplicações incluem:
Indústria | Aplicações |
Aeronáutica | Produção de componentes de motores a jato, pás de turbinas e componentes estruturais de alta precisão. |
Médica | Fabricação de implantes, instrumentos cirúrgicos e dispositivos médicos de precisão. |
Automotiva | Produção de componentes de motores de alto desempenho, como válvulas e componentes do sistema de injeção de combustível. |
Roller Burnishing
O roller burnishing é um processo de acabamento de superfície que utiliza rolos de aço polidos para deformar plasticamente a superfície de uma peça de trabalho, resultando em um acabamento liso e espelhado. Esse método é amplamente valorizado por sua capacidade de melhorar a qualidade superficial sem a necessidade de remoção de material.
Explicação de Como Funciona o Processo de Roller Burnishing
O processo de roller burnishing envolve a aplicação de rolos de aço polidos sobre a superfície da peça de trabalho. Sob alta pressão, esses rolos comprimem a superfície, causando uma deformação plástica controlada. Esta deformação fecha microfissuras e rugosidades, resultando em uma superfície extremamente lisa.
Os principais componentes do processo incluem:
- Rolos de Aço Polidos: Ferramentas cilíndricas que aplicam pressão à superfície da peça de trabalho.
- Peça de Trabalho: O material que será submetido ao processo de roller burnishing.
- Máquina de Burnishing: Equipamento que aplica a força necessária para pressionar os rolos contra a peça de trabalho.
Resultados Obtidos com o Uso de Rolos de Aço Polidos
- Acabamento Espelhado: A superfície da peça de trabalho adquire um acabamento extremamente liso e brilhante, semelhante a um espelho.
- Melhoria na Resistência à Fadiga: O processo aumenta a resistência à fadiga da peça ao reduzir as microfissuras e outras imperfeições superficiais.
- Redução de Porosidade: A compressão da superfície diminui a porosidade, resultando em uma peça mais densa e resistente.
- Precisão Dimensional: O roller burnishing melhora a precisão dimensional da peça de trabalho, garantindo que as dimensões finais estejam dentro das tolerâncias especificadas.
Indicação para Materiais Mais Macios e Acabamento Espelhado
O roller burnishing é especialmente indicado para materiais mais macios, como alumínio, cobre, latão e aços macios. Esses materiais respondem bem à deformação plástica, permitindo que o processo alcance um acabamento espelhado com eficiência.
Material | Aplicabilidade |
Alumínio | Produção de componentes automotivos e aeroespaciais com alta precisão e acabamento liso. |
Cobre | Fabricação de peças de conexão elétrica, onde a condutividade e o acabamento superficial são críticos. |
Latão | Componentes de instrumentos musicais e válvulas que requerem um acabamento estético superior. |
Aços Macios | Aplicações em moldes e matrizes que necessitam de alta durabilidade e acabamento superficial. |
Usinagem por Jato de Água
A usinagem por jato de água é uma técnica inovadora que utiliza a força de jatos de água de alta pressão para cortar materiais em chapas. Essa tecnologia é amplamente reconhecida por sua capacidade de realizar cortes precisos e limpos, sem a necessidade de calor ou abrasivos químicos.
Descrição do Processo de Usinagem por Jato de Água
O processo de usinagem por jato de água envolve a utilização de um bocal de alta pressão que dispara um jato de água extremamente fino e rápido contra a superfície do material a ser cortado. Esse jato, que pode incluir partículas abrasivas em alguns casos, é capaz de cortar uma variedade de materiais com alta precisão.
Os principais componentes do sistema de usinagem por jato de água incluem:
- Bomba de Alta Pressão: Gera a pressão necessária para o jato de água.
- Bocal de Corte: Direciona o jato de água de alta pressão para o ponto de corte.
- Tanque de Abrasivo: (Opcional) Adiciona partículas abrasivas ao jato de água para cortar materiais mais duros.
- Sistema de Controle CNC: Controla a trajetória e a velocidade do jato de água para cortes precisos.
Vantagens do Uso de Jatos de Alta Pressão para Cortar Materiais em Chapas
- Versatilidade: Capaz de cortar uma ampla gama de materiais, incluindo metais, cerâmicas, compósitos e vidros.
- Ausência de Deformação Térmica: Como o processo não gera calor significativo, não há risco de deformação térmica ou alterações nas propriedades do material.
- Segurança e Sustentabilidade: O uso de água como meio de corte elimina a necessidade de produtos químicos nocivos, tornando o processo mais seguro e ambientalmente amigável.
- Redução de Resíduos: A precisão do corte minimiza a geração de resíduos, resultando em um processo mais eficiente e econômico.
Precisão e Limpeza das Peças Produzidas
Uma das maiores vantagens da usinagem por jato de água é a alta precisão e limpeza das peças cortadas. A capacidade de realizar cortes finos e detalhados com tolerâncias apertadas torna essa técnica ideal para aplicações onde a qualidade do acabamento é crucial.
Material | Aplicabilidade |
Aço Inoxidável | Produção de componentes médicos e alimentícios com alta precisão e sem contaminação térmica. |
Alumínio | Indústria aeroespacial e automotiva, onde a precisão e a integridade do material são essenciais. |
Compósitos | Fabricação de peças para a indústria de aviação e esportes, onde cortes limpos e sem danos são necessários. |
Vidro | Criação de designs arquitetônicos complexos e precisos, sem rachaduras ou quebras. |
Usinagem Híbrida
A usinagem híbrida representa uma inovação significativa na manufatura moderna, combinando técnicas tradicionais de usinagem com processos de manufatura aditiva. Esse método permite a criação de peças com geometrias complexas e o uso eficiente de materiais de alto custo, oferecendo vantagens únicas para diversas indústrias.
Definição do Processo de Usinagem Híbrida
A usinagem híbrida é definida como a integração de processos de usinagem subtrativa e aditiva em uma única máquina-ferramenta ou sistema de manufatura. O objetivo é aproveitar os pontos fortes de ambos os métodos para alcançar resultados que seriam difíceis ou impossíveis com apenas um deles.
Os principais componentes de um sistema de usinagem híbrida incluem:
- Módulo de Usinagem Subtrativa: Equipado com ferramentas de corte convencionais para remover material de forma precisa.
- Módulo de Manufatura Aditiva: Utiliza técnicas como a deposição de material por laser ou jato de pó para adicionar material camada por camada.
- Sistema de Controle CNC: Coordena a interação entre os módulos subtrativo e aditivo para garantir a precisão e a qualidade do produto final.
Combinação de Técnicas Tradicionais com Manufatura Aditiva
A combinação de técnicas tradicionais com manufatura aditiva permite uma série de benefícios, incluindo:
- Flexibilidade de Design: A capacidade de adicionar material camada por camada permite a criação de geometrias internas complexas, canais de resfriamento conformais e outras características que seriam difíceis de alcançar com a usinagem tradicional.
- Redução de Resíduos: A adição de material apenas onde é necessário minimiza o desperdício de material, tornando o processo mais sustentável e econômico.
- Reparo e Recondicionamento: Peças danificadas podem ser reparadas adicionando material nas áreas desgastadas ou danificadas, prolongando a vida útil dos componentes e reduzindo os custos de substituição.
Exemplos de Geometrias Complexas e Uso Mais Eficiente de Materiais Caros
A usinagem híbrida permite a criação de peças com geometrias complexas que seriam impossíveis de fabricar com métodos tradicionais. Alguns exemplos incluem:
Indústria | Aplicação |
Aeroespacial | Componentes de motores a jato com canais de resfriamento internos complexos para melhorar a eficiência térmica. |
Médica | Implantes ortopédicos personalizados com estruturas de suporte internas para promover a integração com o osso. |
Automotiva | Peças de motores e transmissões com geometrias otimizadas para reduzir o peso e aumentar a eficiência do combustível. |
Energia | Pás de turbinas eólicas com perfis aerodinâmicos complexos para maximizar a captação de energia. |
Além disso, a usinagem híbrida permite o uso mais eficiente de materiais caros, como ligas de titânio e superligas de níquel, ao adicionar material apenas onde é necessário e removê-lo com precisão onde não é.
Outros Processos Não Convencionais
Além dos processos de usinagem previamente discutidos, existem outros métodos menos comuns, mas igualmente inovadores, que estão ganhando espaço na indústria. Estes incluem a usinagem por feixe de elétrons, fotoquímica, química, jato de água abrasivo e plasma. Cada um desses processos oferece vantagens únicas que podem ser exploradas em aplicações específicas.
Usinagem por Feixe de Elétrons
A usinagem por feixe de elétrons utiliza um feixe concentrado de elétrons acelerados para remover material de uma peça. O feixe de elétrons gera calor intenso ao atingir a superfície do material, vaporizando-o instantaneamente.
- Aplicações: Ideal para materiais super duros e componentes de alta precisão, como os utilizados na indústria aeroespacial e eletrônica.
- Vantagens: Alta precisão, capacidade de trabalhar com materiais extremamente duros e produção de cortes limpos sem contato físico.
Usinagem Fotoquímica
A usinagem fotoquímica envolve a aplicação de uma máscara fotossensível sobre a superfície do material. Áreas expostas à luz UV são quimicamente alteradas e depois removidas por um processo de gravação química.
- Aplicações: Produção de circuitos impressos, componentes de microssistemas e gravação de superfícies complexas.
- Vantagens: Alta precisão em padrões complexos, capacidade de produzir peças em grande escala e baixo custo para produções em massa.
Usinagem Química
A usinagem química envolve a remoção de material através de reações químicas controladas. O material é exposto a um agente químico que dissolve seletivamente certas áreas.
- Aplicações: Fabricação de componentes delicados, como folhas metálicas finas e microcomponentes.
- Vantagens: Remoção de material sem estresse mecânico, alta precisão em peças pequenas e complexas e capacidade de trabalhar com materiais sensíveis ao calor.
Usinagem por Jato de Água Abrasivo
A usinagem por jato de água abrasivo combina a força de um jato de água de alta pressão com partículas abrasivas para cortar materiais duros.
- Aplicações: Corte de metais, cerâmicas, vidros e materiais compostos em chapas.
- Vantagens: Cortes precisos e limpos, sem zonas afetadas pelo calor, e capacidade de cortar uma ampla variedade de materiais.
Usinagem por Plasma
A usinagem por plasma utiliza um arco elétrico para ionizar um gás, criando um plasma quente que derrete e remove material.
- Aplicações: Corte de metais, especialmente aços inoxidáveis e alumínio, e soldagem de componentes metálicos.
- Vantagens: Alta velocidade de corte, capacidade de cortar materiais espessos e produção de cortes limpos com pouca distorção.
Ao longo deste artigo, exploramos diversos processos de usinagem não convencionais que têm revolucionado a indústria moderna. Entre eles, destacamos a usinagem a laser, usinagem ultrassônica, usinagem eletroquímica, roller burnishing, usinagem por jato de água e usinagem híbrida. Cada um desses processos oferece vantagens específicas, desde a precisão e a capacidade de trabalhar com materiais frágeis até a eficiência e a economia de materiais caros.
Estes métodos inovadores são fundamentais para atender às demandas crescentes por produtos de alta qualidade e precisão, especialmente em setores como a aeronáutica, automotivo e eletrônico. A versatilidade e a eficiência dos processos de usinagem não convencionais permitem a fabricação de peças complexas e de alta performance, garantindo a competitividade das empresas no mercado global.
O futuro da usinagem promete avanços ainda mais significativos, com tendências como a integração de tecnologias digitais, o uso de materiais avançados e a automação ganhando destaque. Investir em tecnologias de usinagem não convencionais é essencial para se manter à frente no mercado e garantir a produção de componentes de alta qualidade e custo-efetivos.